Mill Turn Machining
Optimal for High Mix, Low Volume Complex Parts
Owens Industries is a leader in precision mill turning. Our team leverages advanced CNC machining to seamlessly integrate milling and turning operations with unparalleled efficiency. With Owens, you gain access to cutting-edge precision manufacturing capabilities for intricate geometries and diverse materials. Our Mill-Turning expertise delivers reliable components machined with high precision.
Have problem parts or impossible components? In a hurry? Call on the expertise of Owens. Our commitment to quality and customer satisfaction sets us apart.
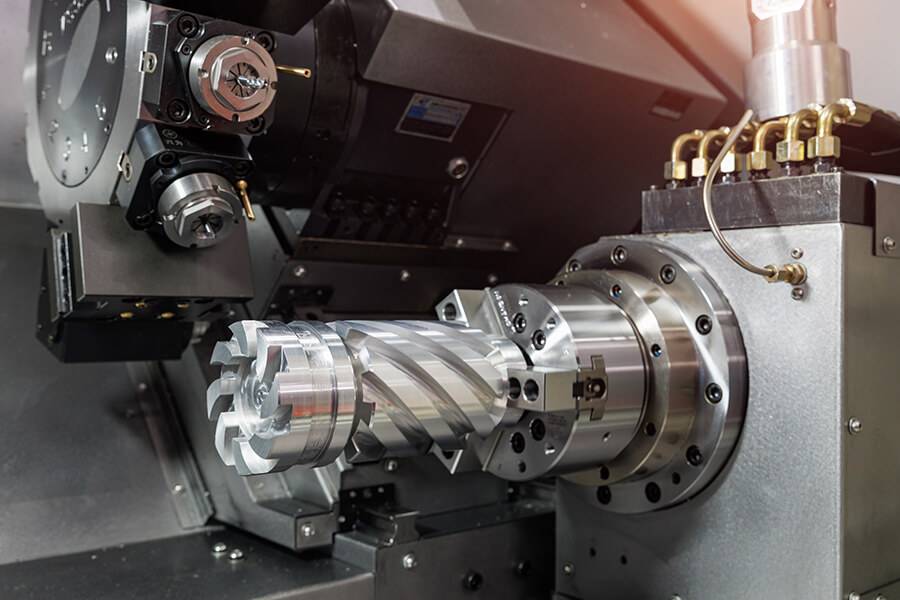
What is Mill Turning?
Mill-Turning seamlessly integrates milling and turning operations, streamlining manufacturing processes. This advanced CNC machining technique eliminates the need for multiple setups, boosting efficiency. Simultaneous turning and milling, along with the ability to handle intricate geometries, make Mill-Turning a practical choice for precision manufacturing.
As a workpiece rotates, the Mill-Turn machine executes rotating tooling operations such as cross-drilling, tapping, slotting, and milling simultaneously. This eliminates the need for multiple setups and reduces downtime associated with changing between different machining centers. This innovative approach not only accelerates part production but also maintains high accuracy, making Mill-Turning an incredible option for precision manufacturing at Owens Industries.
Why Choose Owens Industries for Mill-Turning
Our specialized mill-turn machining process is meticulously executed, ensuring exacting precision for each component. Utilizing cutting-edge CNC technology, we seamlessly integrate turning and milling operations, achieving unparalleled machining tolerances. The simultaneous execution of multiple operations in a single setup enhances efficiency, enabling the mill-turn machines to handle complex workpieces seamlessly. From intricate geometries to diverse materials, our mill-turn expertise ensures optimal results without the need for additional finishing.
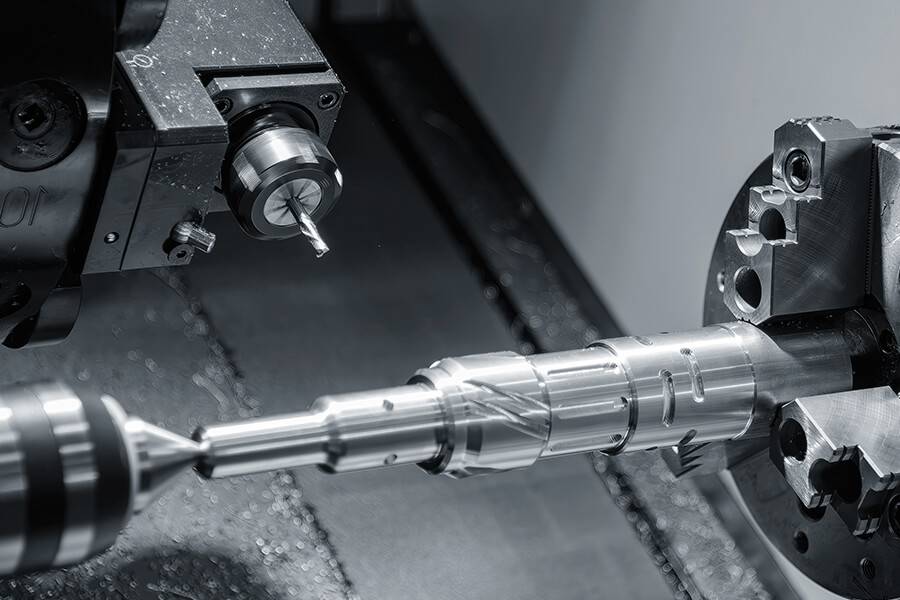
View our Success Gallery to see our work!
Benefits of Multi-Axis Mill-Turn Machining
Mill-turn machining stands out as a revolutionary process that combines turning and milling operations into a single, highly efficient workflow.
- Single-Setup Efficiency: Mill-turn technology completes complex parts in a single setup, reducing the need for multiple machines and minimizing errors. Its true multitasking capability, turning workpieces while simultaneously executing rotating tooling operations, leads to faster production and reduced setup times.
- Swift Production: Mill-turn machines facilitate rapid transitions from concept to final product, ensuring faster time-to-market and reduced lead times. Mill-turn technology also allows for early optimization of part designs, ensuring efficiency and cost-effectiveness in the machining process.
- Enhanced Precision: Integrating turning and milling minimizes repositioning, leading to improved accuracy with tight tolerances as fine as +/- .0001. Mill-turn machining excels in the creation of intricate part geometries, offering a solution for components with complex shapes and features.
- Material Versatility: Capable of handling a wide range of materials, from common metals to superalloys, making it suitable for diverse industries.
Mill Turning vs Milling and Turning
Milling and turning are individual CNC machining processes, each with its unique characteristics and applications. However, the combination of these processes in mill-turn machining introduces an approach that offers advantages over separate milling and turning operations. Mill turning is characterized by its integration of milling and turning capabilities within a single-machine setup. This process efficiently handles complex parts by simultaneously performing milling and turning operations.
When milling and turning are executed separately, the machining operations are divided between dedicated machines. Milling involves a rotating cutting tool removing material while turning centers around a rotating workpiece with a stationary cutting tool. While effective for specific operations, this approach may necessitate transferring workpieces between machines, leading to increased setup and handling times. In CNC lathe machining and turning, the workpiece is held in place by a chuck and rotated at high speeds while the cutting tools are brought into contact with the workpiece to remove material and create the desired shape.
The choice between mill turning and separate milling and turning processes depends on the project's requirements. Mill turning stands out for its efficiency in handling complex parts, minimizing setup times, and offering a consolidated approach to machining operations.
Materials
Mill-Turning Materials Trusted by Owens Industries
Our extensive range of material capabilities guarantees that we can satisfy the varied and particular needs of our clients in a variety of industries. Owens Industries has extensive experience manufacturing parts from different materials using Mill-Turning manufacturing:
- Brass
- Copper
- Stainless Steel
- Tool Steel
- Alloy Steel
- Aluminum
- Hastelloy
- Inconel
- Invar
- Maraging Steel
- Titanium
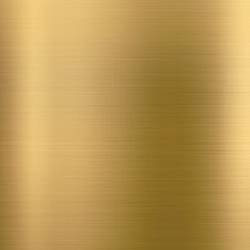
Brass
Brass is a metal known for its easy machinability and good electrical conductivity. It is ideal for applications requiring low friction, such as gears, locks, and musical instruments.
Brass | UNS Designation | DIN Designation | Alternative Designation |
---|---|---|---|
C36000 | UNS C36000 | CUZN39PB3 | CuZn39Pb3 |
C46400 | UNS C46400 | CuZn38Al | Naval Brass |
C93200 | UNS C93200 | Saems 660 | Bearing Bronze |
C48500 | UNS C48500 | CuZn39Sn1 | Leaded Muntz Metal |
C26000 | UNS C26000 | CUZN30 | Cartridge Brass |
C37700 | UNS C37700 | CUZN40PB2 | Forging Brass |
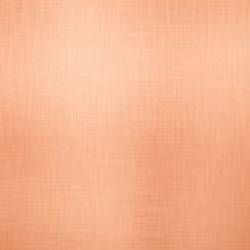
Copper
Copper is excellent at conducting heat and electricity, making it perfect for electrical uses like busbars and wire connectors. It is easily recognized by its shiny reddish-orange color and is also used in plumbing and roofing.
Copper | UNS Designation | DIN Designation | Alternative Designation |
---|---|---|---|
C11000 | UNS C11000 | Cu-ETP | Electrolytic Tough Pitch (ETP) Copper |
C10100 | UNS C10100 | OF-OK | Oxygen-Free Electronic (OFE) Copper |
C10200 | UNS C10200 | OF-Cu | Oxygen-Free (OF) Copper |
C28000 | UNS C28000 | CuZn40 | Muntz Metal |
C14500 | UNS C14500 | TeCu | Tellurium Copper |
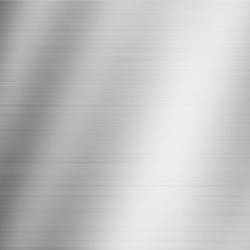
Stainless Steel
Stainless steel is known for its strength, heat, and corrosion resistance, along with its durability and attractive appearance. These qualities make it suitable for a wide range of uses, including kitchenware, medical instruments, and construction.
Stainless Steel | UNS Designation | DIN Designation | Alternative Designation |
---|---|---|---|
316L | UNS S31603 | X2CrNiMo17-12-2 | Stainless Steel 316L |
304 | UNS S30400 | X5CrNi18-10 | Stainless Steel 304 |
17-4 PH | UNS S17400 | X5CrNiCuNb16-4 | Stainless Steel 17-4 PH |
303 | UNS S30300 | X8CrNiS18-9 | Stainless Steel 303 |
420 | UNS S42000 | X20Cr13 | Stainless Steel 420 |
440C | UNS S44004 | X105CrMo17 | Stainless Steel 440C |
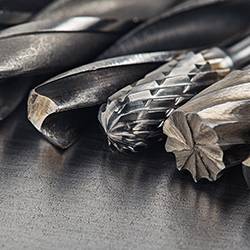
Tool Steel
Tool steels are hard, stiff, and resistant to abrasion, making them perfect for manufacturing industrial tools. Their robustness is essential for cutting, drilling, and molding applications in various industries.
Tool Steel | UNS Designation | DIN Designation | Alternative Designation |
---|---|---|---|
D2 | UNS T30402 | 1.2379 | X155CrVMo12-1 |
M2 | UNS T11302 | 1.3343 | HS6-5-2C |
A2 | UNS T30102 | 1.2363 | X100CrMoV5-1 |
S7 | UNS T41907 | 1.2355 | 50CrMoV13-15 |
O1 | UNS T31501 | 1.2510 | 100MnCrW4 |
H13 | UNS T20813 | 1.2344 | X40Cr |
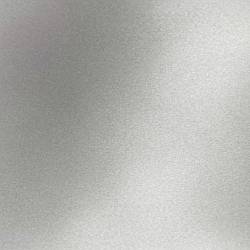
Alloy Steel
Alloy steels include additional elements beyond carbon, which improve their hardness, toughness, and resistance to fatigue and wear. These steels are widely used in construction, automotive, and machinery due to their enhanced properties.
Alloy Steel | UNS Designation | DIN Designation | ISO Designation |
---|---|---|---|
4140 | 1.7225 | 708M40 | 42CrMo4 |
4340 | 1.6565 | 817M40 | 40NiCrMo6 |
8620 | 1.6523 | 805M20 | 20NiCrMo2 |
52100 | 1.3505 | 100Cr6 | SUJ2 |
4142 | 1.7227 | 708M40T | 41CrMoS4 |
6150 | 1.8159 | 735A51 | 50CrV4 |
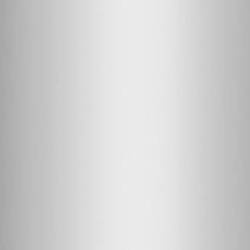
Aluminum
Aluminum alloys are lightweight and strong, with excellent thermal and electrical conductivity. They are also resistant to corrosion and can be anodized for added protection, making them ideal for aerospace and packaging industries.
Aluminum Alloy | UNS Designation | DIN Designation | ISO Designation |
---|---|---|---|
7075-T651 | 3.4365 | 76528 | AlZn5.5MgCu |
6082-T651 | 3.2315 | 64430 | AlSi1MgMn |
6060 | 3.3206 | EN AW-6060 | AlMgSi |
5052 | EN AW-5052 | 3.3523 | AlMg2,5 |
2017A | 3.1325 | 24530 | AlCu4MgSi |
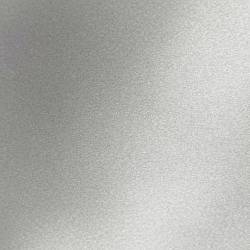
Hastelloy
Hastelloy is a group of nickel alloys known for their high resistance to corrosion, pitting, and stress-corrosion cracking. They are often used in harsh environments like chemical processing and aerospace, where durability is crucial.
Hastelloy | UNS Designation | DIN Designation | Alternative Designation |
---|---|---|---|
C276 | UNS N10276 | 2.4819 | NiMo16Cr15W |
C22 | UNS N06022 | 2.4602 | NiCr21Mo14W |
B-2 | UNS N10665 | 2.4617 | NiMo28 |
X | UNS N06002 | 2.4665 | NiCr22Fe18Mo |
C2000 | UNS N06200 | 2.4675 | NiCr23Mo16Cu |
G-30 | UNS N06030 | 2.4603 | NiCr29Mo9Fe |
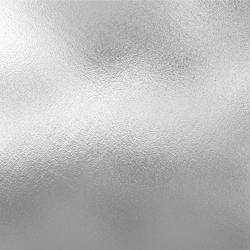
Inconel
Inconel is a strong, corrosion-resistant nickel alloy, ideal for challenging aerospace applications. It can withstand extreme temperatures and pressures, making it suitable for jet engines and gas turbines.
Inconel | UNS Designation | DIN Designation | Alternative Designation |
---|---|---|---|
718 | UNS N07718 | 2.4668 | NiCr19Fe19Nb5Mo3 |
625 | UNS N06625 | 2.4856 | NiCr22Mo9Nb |
600 | UNS N06600 | 2.4816 | NiCr15Fe |
X-750 | UNS N07750 | 2.4669 | NiCr15Fe7TiAl |
601 | UNS N06601 | 2.4851 | NiCr23Fe |
725 | UNS N07725 | 2.4668 | NiCr19Fe19Nb5Mo3 |
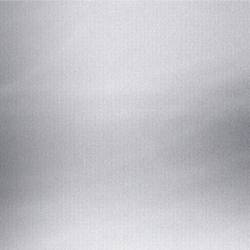
Invar
Invar is a nickel alloy with very low thermal expansion, making it highly stable and perfect for precision applications such as instrumentation and aerostructure molds. It is also used in scientific instruments where dimensional stability is critical.
Invar | UNS Designation | DIN Designation | Alternative Designation |
---|---|---|---|
36 | UNS K93600 | 1.3912 | FeNi36 |
42 | UNS K94200 | 1.3917 | FeNi42 |
48 | UNS K94800 | 1.3922 | FeNi48 |
32-5 | UNS K94610 | 1.3911 | FeNi32-5 |
42-6 | UNS K94620 | 1.3913 | FeNi42-6 |
46 | UNS K94630 | 1.3914 | FeNi46 |
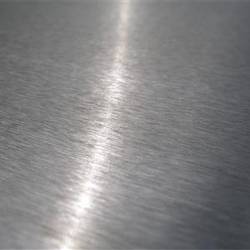
Maraging Steel
Maraging steels are ultra-high-strength steels that are easy to machine and weld without causing distortion. They gain their exceptional hardness and toughness from a special heat-treating process, making them suitable for aerospace and tooling applications.
Maraging Steel | UNS Designation | DIN Designation | Alternative Designation |
---|---|---|---|
200 | UNS K93120 | 1.6359 | 20Ni Maraging Steel C200 |
250 | UNS K92890 | 1.6358 | 18Ni Maraging Steel C250 |
300 | UNS K93120 | 1.6354 | 18Ni Maraging Steel C300 |
350 | UNS K93160 | 1.6356 | 18Ni Maraging Steel C350 |
400 | UNS K91460 | 1.6352 | Custom 465 Stainless |
500 | UNS K92810 | 1.6354 | Custom Age 625 Plus |
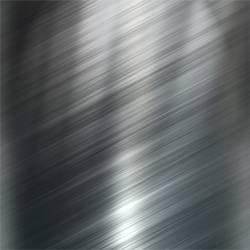
Titanium
Titanium is a lightweight metal with excellent strength, low thermal expansion, and high corrosion resistance. Its ability to be sterilized and its biocompatibility make it unique, especially in medical implants and aerospace components.
Titanium Grade | UNS Designation | DIN Designation | Alternative Designation |
---|---|---|---|
5 (Ti-6Al-4V) | UNS R56400 | 3.7165 | Ti-6Al-4V |
2 | UNS R50400 | 3.7035 | CP Titanium |
23 (Ti-6Al-4V ELI) | UNS R56401 | 3.7165 | Ti-6Al-4V ELI |
9 (Ti-3Al-2.5V) | UNS R56320 | 3.7195 | Ti-3Al-2.5V |
7 (Ti-0.2Pd) | UNS R52400 | 3.7235 | Ti-0.2Pd |
12 (Ti-0.3Mo-0.8Ni) | UNS R53400 | 3.7105 | Ti-0.3Mo-0.8Ni |
Tolerances
Owens Industries’ Achievable Mill-Turn Machining Tolerances
Our mill-turn machining service offers exceptional precision for components that require both milling and turning operations in a single setup. With tolerances as tight as ±0.0005 inches, mill-turn machining combines multiple processes to create parts that are both accurate and cost-effective. This service accommodates part sizes up to 14" diameter and 16" overall length, with a standard lead time of 12 weeks. Mill-turn machining is ideal for high-quality, intricate parts in industries like oil & gas and pharmaceuticals, where durability and dimensional accuracy are paramount.
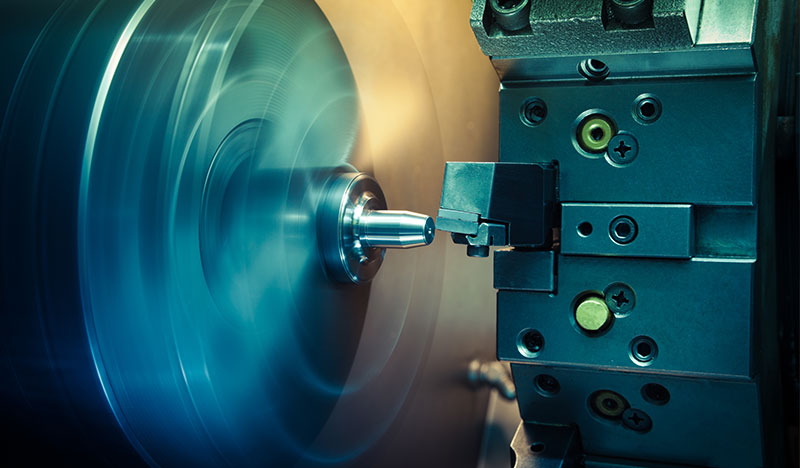
Attribute | Value |
---|---|
Maximum Part Size | 14" dia x 16" oal |
Standard Lead Time | 12 weeks |
General Tolerances | .0025" |
Precision Tolerances | .0005" |
Minimum Feature Size | .060" dia x .050" oa |
Minimum Surface Finish | 8 |
Standard Surface Finish | 32 |
*Standard delivery dependent on workloads. Call Owens for current lead times.
Industries
Mill-Turning Industries Trusted by Owens Industries
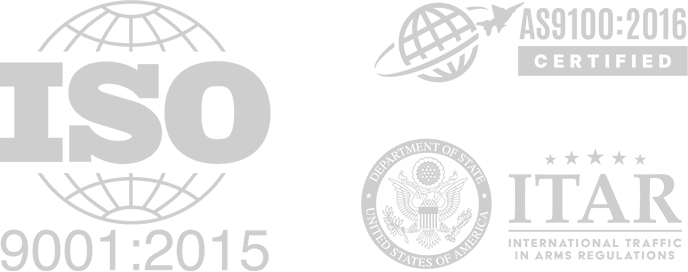
FAQ
Mill Turn Machining Frequently Asked
Questions
What is Mill Turning, and how does it differ from traditional machining processes?
Mill Turning is an advanced CNC technique integrating milling and turning in one setup, streamlining processes and reducing errors compared to traditional methods.
What are the key benefits of choosing Mill Turn Machining for complex parts?
Mill Turning offers single-setup efficiency, true multitasking, and versatility, accelerating production, reducing setup times, and ensuring precision for diverse industries.
How does Mill Turning compare to separate milling and turning processes?
Mill Turning efficiently handles complex parts by integrating milling and turning in a single machine setup, streamlining processes and reducing production time compared to separate operations.
Why choose Owens Industries for Mill-Turning services?
Owens Industries ensures meticulous execution and precision in Mill Turning, utilizing cutting-edge CNC technology for seamless integration and handling of complex workpieces.
What materials does Owens Industries use for Mill-Turning, and how are they selected?
Owens Industries uses materials like alloy steel, aluminum, brass, bronze, carbon steel, copper, hardened steel, and Hastelloy, selecting them based on specific properties to meet project requirements and ensure precision machining.