Additive Manufacturing
Achieve the Impossible While Reducing Cost with Owens Industries
Owens Industries combines over seven decades of expertise in precision manufacturing with cutting-edge additive manufacturing technologies to produce complex parts. We provide nationwide precision additive manufacturing services with unmatched quality and innovation for companies in the aerospace and defense sectors. Our specialized additive manufacturing capabilities, combined with traditional machining techniques, let us create complex geometries, lightweight components and custom parts with superior precision.
Have problem parts or impossible components? In a hurry? Call on the expertise of Owens.
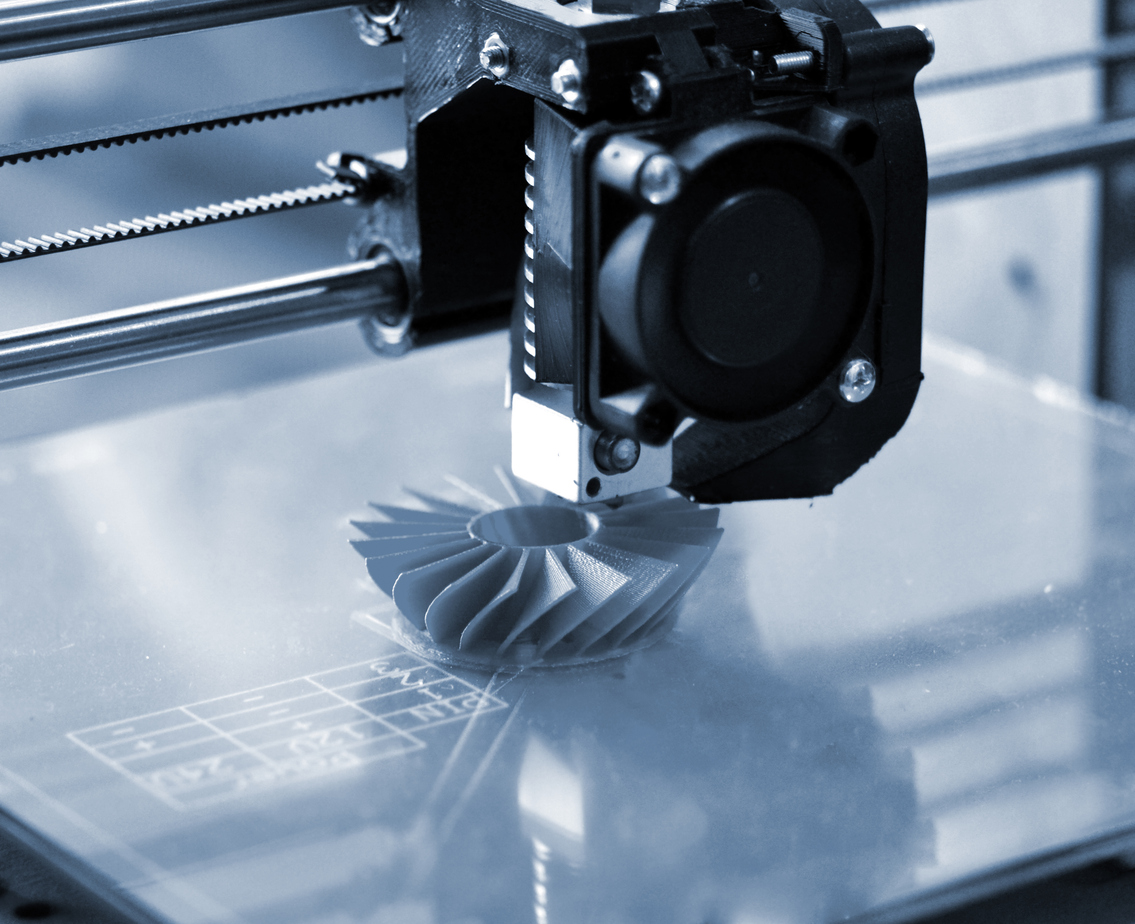
What is Additive Manufacturing?
Additive Manufacturing, commonly known as 3D printing, is a production process used to create objects layer by layer from digital models. This process contrasts with traditional subtractive manufacturing methods like CNC machining, where the material is removed from a larger block.
Additive manufacturing allows for intricate designs found difficult or impossible to produce using conventional methods. Additive manufacturing technologies can use a wide range of materials, including Hastelloy, Kovar, Molybdenum and Invar, serving as a versatile solution for aerospace and defense industry parts.
Additive Manufacturing Benefits Over Traditional CNC Machining
- Design Freedom: Additive manufacturing produces intricate geometries like internal pockets, lattice structures and organic shapes. They are difficult to achieve with subtractive CNC machining.
- Reduced Waste: Additive processes use only the necessary material, building parts layer by layer, significantly reducing waste compared to CNC's material removal approach.
- Accelerated Product Development: Additive manufacturing provides rapid prototyping, faster design iterations and quicker time-to-market.
- Lightweight Structures: Additive techniques support the creation of lightweight structures without sacrificing strength, benefiting industries like aerospace and defense.
- Cost Efficiency: For low-volume production runs, additive manufacturing can be more cost-effective than traditional CNC machining, which requires specific tooling.
Why Choose Owens Industries for Additive Manufacturing?
Owens Industries utilizes state-of-the-art additive manufacturing equipment for high-precision production of complex parts through advanced 3D printing technologies. Our team of engineers and machinists brings a wealth of experience to each project, guaranteeing every component meets exacting specifications. Operating out of an ISO-certified facility, we adhere to the highest industry standards for quality and safety.
Our process involves robust testing for all printed parts to meet stringent standards. We implement comprehensive quality control measures, including visual inspections and non-destructive testing methods, to validate the integrity and performance of each component.
By choosing Owens Industries, you gain a partner fully dedicated to innovation and excellence.
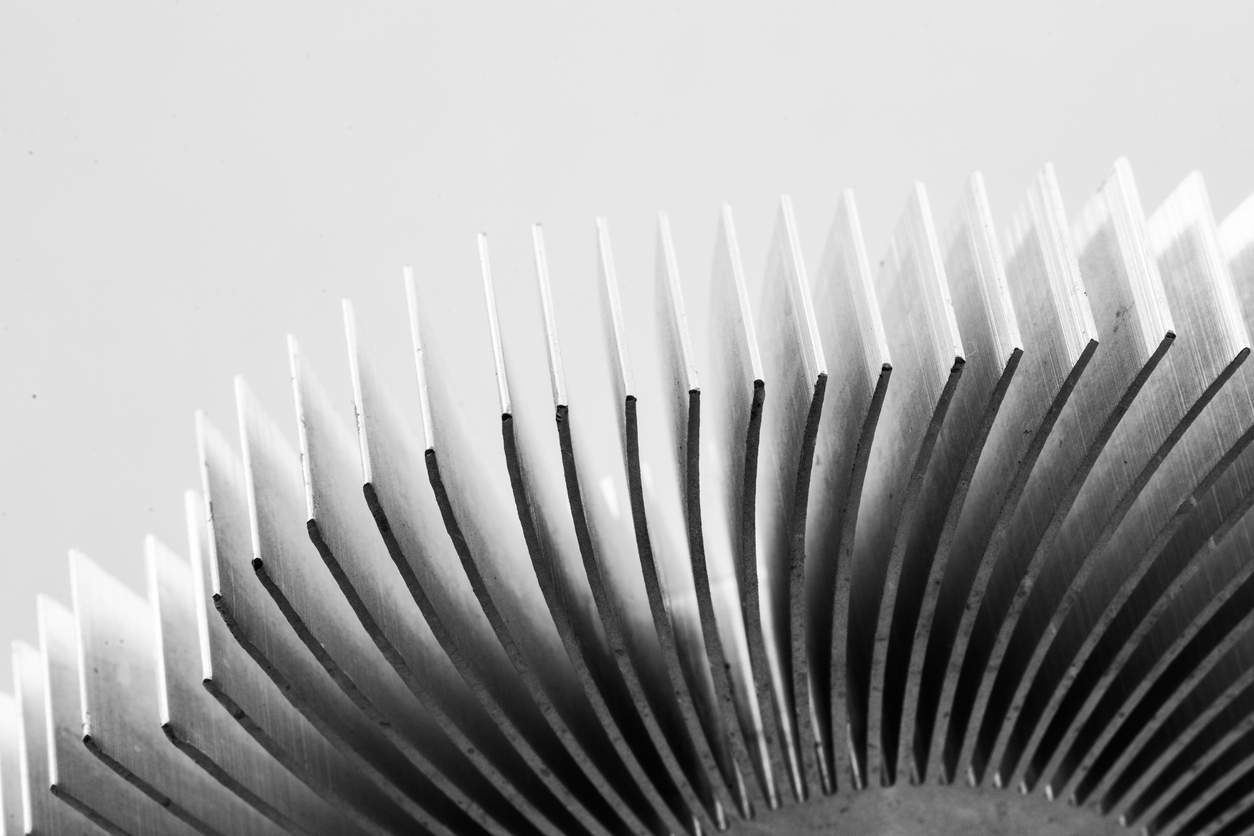
View our Success Gallery to see our work!
Additive Manufacturing Applications in Aerospace & Defense
Complex Rocket Parts
Additive manufacturing transforms the production of intricate rocket components. The ability to create complex geometries allows for high-performance engine parts with significantly reduced production times. This technology facilitates rapid design iterations, optimizing performance and reliability without the limitations of traditional manufacturing methods.
Lightweight Aircraft Components
In aerospace, additive manufacturing produces lightweight components for better fuel efficiency and overall aircraft performance. Redesigning parts using advanced 3D printing techniques helps manufacturers achieve substantial weight reductions. These innovations lead to lower operational costs and improved fuel economy, making the parts essential for modern aircraft design.
End-Use Parts for Unmanned Aerial Systems
Additive manufacturing is crucial in producing flight-qualified parts for unmanned aerial systems (UAS). This approach accelerates production while meeting stringent aerospace standards. Rapid prototyping capabilities allow quick adaptation to evolving mission requirements, deploying UAS effectively and efficiently.
Custom Tooling Solutions
Additive manufacturing extends to tooling processes in aerospace and defense. Custom jigs and fixtures produced through 3D printing enhance precision during assembly operations. This innovative approach improves efficiency and quality in production workflows, allowing manufacturers to meet exact specifications easily.
Rapid Prototyping for Defense Applications
Additive manufacturing modernizes operational capabilities through rapid prototyping. This technology supports on-demand production of critical components, enabling military units to adapt quickly to battlefield requirements. Reduced lead times enhance material readiness and operational effectiveness, keeping defense operations agile.
Maintenance, Repair & Operations (MRO)
Additive manufacturing is vital for maintenance, repair and operations within the aerospace and defense sectors. On-demand production of spare parts minimizes equipment downtime and boosts operational readiness. Components with long lead times or difficult sourcing can be produced swiftly using 3D printing technology, keeping military and commercial equipment operational without delays.
Materials
Additive Manufacturing Material Capabilities
Additive Manufacturing uses various materials including Hastelloy, Kovar, Molybdenum and Invar. Owens Industries has extensive experience manufacturing parts from different materials using additive manufacturing.
- Stainless Steel
- Aluminum
- Inconel
- Titanium
- Hastelloy
- Invar
- Kovar
- Molybdenum
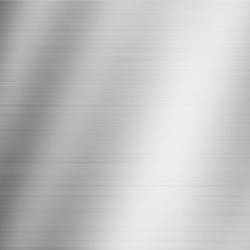
Stainless Steel
Stainless steel is known for its strength, heat, and corrosion resistance, along with its durability and attractive appearance. These qualities make it suitable for a wide range of uses, including kitchenware, medical instruments, and construction.
Stainless Steel | UNS Designation | DIN Designation | Alternative Designation |
---|---|---|---|
316L | UNS S31603 | X2CrNiMo17-12-2 | Stainless Steel 316L |
304 | UNS S30400 | X5CrNi18-10 | Stainless Steel 304 |
17-4 PH | UNS S17400 | X5CrNiCuNb16-4 | Stainless Steel 17-4 PH |
303 | UNS S30300 | X8CrNiS18-9 | Stainless Steel 303 |
420 | UNS S42000 | X20Cr13 | Stainless Steel 420 |
440C | UNS S44004 | X105CrMo17 | Stainless Steel 440C |
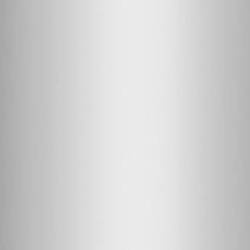
Aluminum
Aluminum alloys are lightweight and strong, with excellent thermal and electrical conductivity. They are also resistant to corrosion and can be anodized for added protection, making them ideal for aerospace and packaging industries.
Aluminum Alloy | UNS Designation | DIN Designation | ISO Designation |
---|---|---|---|
7075-T651 | 3.4365 | 76528 | AlZn5.5MgCu |
6082-T651 | 3.2315 | 64430 | AlSi1MgMn |
6060 | 3.3206 | EN AW-6060 | AlMgSi |
5052 | EN AW-5052 | 3.3523 | AlMg2,5 |
2017A | 3.1325 | 24530 | AlCu4MgSi |
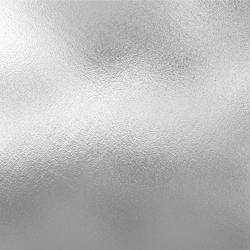
Inconel
Inconel is a strong, corrosion-resistant nickel alloy, ideal for challenging aerospace applications. It can withstand extreme temperatures and pressures, making it suitable for jet engines and gas turbines.
Inconel | UNS Designation | DIN Designation | Alternative Designation |
---|---|---|---|
718 | UNS N07718 | 2.4668 | NiCr19Fe19Nb5Mo3 |
625 | UNS N06625 | 2.4856 | NiCr22Mo9Nb |
600 | UNS N06600 | 2.4816 | NiCr15Fe |
X-750 | UNS N07750 | 2.4669 | NiCr15Fe7TiAl |
601 | UNS N06601 | 2.4851 | NiCr23Fe |
725 | UNS N07725 | 2.4668 | NiCr19Fe19Nb5Mo3 |
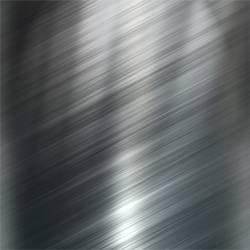
Titanium
Titanium is a lightweight metal with excellent strength, low thermal expansion, and high corrosion resistance. Its ability to be sterilized and its biocompatibility make it unique, especially in medical implants and aerospace components.
Titanium Grade | UNS Designation | DIN Designation | Alternative Designation |
---|---|---|---|
5 (Ti-6Al-4V) | UNS R56400 | 3.7165 | Ti-6Al-4V |
2 | UNS R50400 | 3.7035 | CP Titanium |
23 (Ti-6Al-4V ELI) | UNS R56401 | 3.7165 | Ti-6Al-4V ELI |
9 (Ti-3Al-2.5V) | UNS R56320 | 3.7195 | Ti-3Al-2.5V |
7 (Ti-0.2Pd) | UNS R52400 | 3.7235 | Ti-0.2Pd |
12 (Ti-0.3Mo-0.8Ni) | UNS R53400 | 3.7105 | Ti-0.3Mo-0.8Ni |
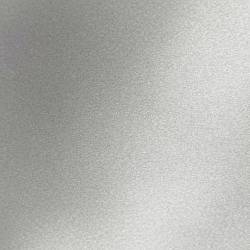
Hastelloy
Hastelloy is a group of nickel alloys known for their high resistance to corrosion, pitting, and stress-corrosion cracking. They are often used in harsh environments like chemical processing and aerospace, where durability is crucial.
Hastelloy | UNS Designation | DIN Designation | Alternative Designation |
---|---|---|---|
C276 | UNS N10276 | 2.4819 | NiMo16Cr15W |
C22 | UNS N06022 | 2.4602 | NiCr21Mo14W |
B-2 | UNS N10665 | 2.4617 | NiMo28 |
X | UNS N06002 | 2.4665 | NiCr22Fe18Mo |
C2000 | UNS N06200 | 2.4675 | NiCr23Mo16Cu |
G-30 | UNS N06030 | 2.4603 | NiCr29Mo9Fe |
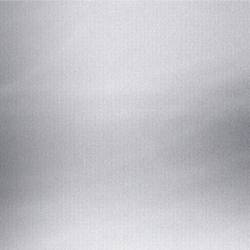
Invar
Invar is a nickel alloy with very low thermal expansion, making it highly stable and perfect for precision applications such as instrumentation and aerostructure molds. It is also used in scientific instruments where dimensional stability is critical.
Invar | UNS Designation | DIN Designation | Alternative Designation |
---|---|---|---|
36 | UNS K93600 | 1.3912 | FeNi36 |
42 | UNS K94200 | 1.3917 | FeNi42 |
48 | UNS K94800 | 1.3922 | FeNi48 |
32-5 | UNS K94610 | 1.3911 | FeNi32-5 |
42-6 | UNS K94620 | 1.3913 | FeNi42-6 |
46 | UNS K94630 | 1.3914 | FeNi46 |

Kovar
Kovar is known for its exceptional thermal stability and precise expansion properties, along with its strength and compatibility with glass-to-metal sealing. These qualities make it ideal for specialized applications in electronics, aerospace, and medical devices.
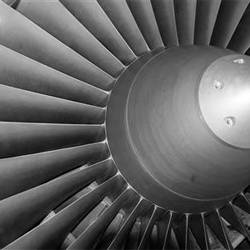
Molybdenum
Molybdenum is known for its high-temperature strength, thermal conductivity, and resistance to corrosion in harsh environments. These qualities make it invaluable for aerospace components, electronic devices, and power generation equipment.
Industries
Additive Manufacturing
Industries Trusted by Owens
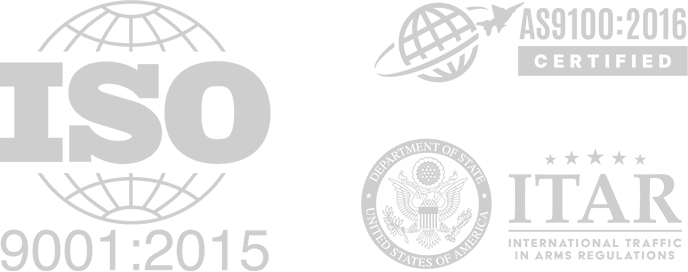
FAQ
Additive Manufacturing Frequently Asked
Questions
How long does it take to produce a part using additive manufacturing?
The production time varies depending on the size, complexity, and material of the part. While small parts can be produced in hours, larger and more complex parts may take several days, especially if post-processing is required.
What industries benefit most from additive manufacturing?
Aerospace, automotive, medical, energy, and industrial sectors benefit greatly from additive manufacturing due to its ability to produce complex, lightweight, and customized parts.
Can additive manufacturing fully replace traditional manufacturing?
While additive manufacturing excels in areas like prototyping and creating complex geometries, it is not likely to replace traditional manufacturing entirely. Both methods have their strengths, and often, a combination of both provides the best solution for certain projects.
What post-processing is required for additive manufacturing parts?
Depending on the material and application, additive manufacturing parts may require post-processing such as heat treatment, CNC machining, surface finishing, or coating to achieve the desired strength, surface quality, and dimensional accuracy.
How accurate is additive manufacturing compared to CNC machining?
While additive manufacturing technology continues to advance in terms of precision, CNC machining generally offers higher accuracy and finer surface finishes. However, additive manufacturing is ideal for creating complex shapes that would be impossible or highly costly using CNC alone.