Deburring
Deburring Completed with Unparalleled Detail
Though deburring can be a fairly simple task, Owens considers it to be an important one. In our deburring department alone, we have employees who have been with us for 30+ years. Each Owens' deburring tech undertakes the microscopic deburring of complex projects with unparalleled attention to detail. And we've developed special finishing compounds for mirror finish polishing and solutions for Electro Polishing. Why call the number of anyone else?
Contact Owens Industries for available deburring part services. Our precision techniques ensure we can work on even the most problematic parts.
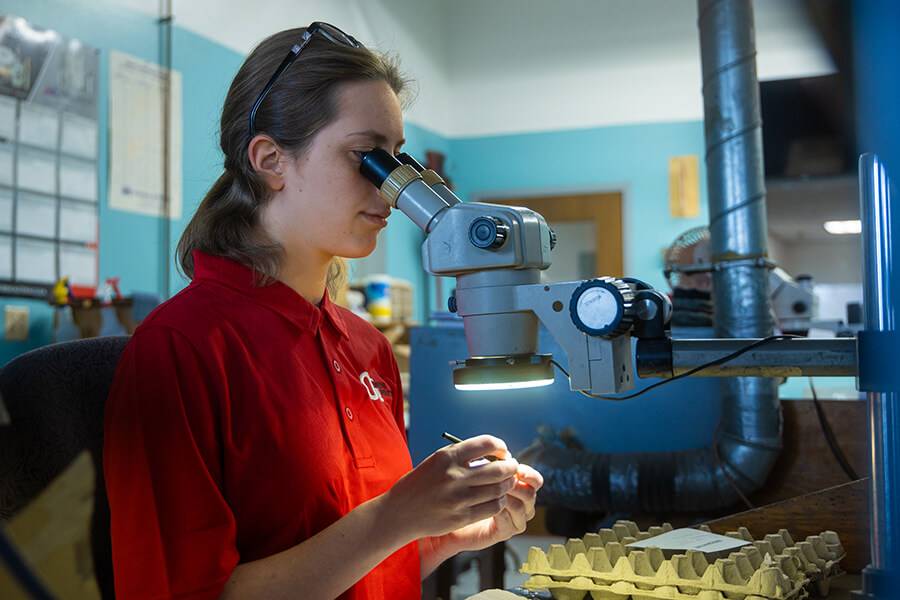
What is Micro CNC Deburring?
CNC deburring, essential in precision machining, addresses the challenge of burrs left on workpieces after CNC machining. Manual CNC deburring involves hand tools like brushes or files, ideal for intricate parts or small batches. Automated CNC deburring uses machines or robots with grinding wheels or abrasive tools, and is more efficient for high-volume production, ensuring both speed and consistency.
The significance of CNC deburring lies in improving fit, functionality, and safety. Deburring ensures precise assembly by eliminating burrs that might hinder components' fit or operation. Additionally, the process enhances safety by removing sharp edges, contributing to overall quality and meeting safety standards.
CNC deburring's impact extends beyond functionality to aesthetics, providing a smoother surface finish that is crucial in industries where visual appeal is a high priority. Deburring is a versatile practice applicable to various materials and industries, promoting long-term cost-efficiency despite initial setup costs.
Why Choose Owens Industries for Micro Deburring?
Owens Industries is your choice for microdeburring services, driven by a commitment to precision and innovation. Our deburring department, with professionals boasting over 30 years of experience, ensures meticulous attention to detail in the microscopic deburring of complex projects. Utilizing cutting-edge technology, we guarantee a mirror finish for each machined part.
In contrast to automated processes, Owens Industries excels in by-hand deburring services, where precision and accuracy are required. Our comprehensive quality control ensures every workpiece meets required standards, minimizing defects and maximizing customer satisfaction. Choose Owens Industries for microdeburring and elevate your expectations for precision and performance.
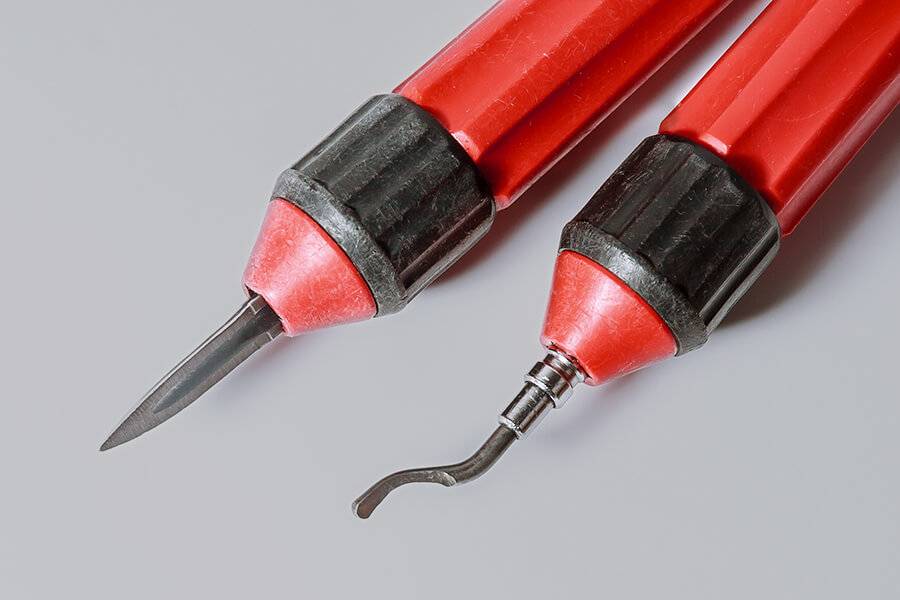
By-Hand Deburring Services
Normal CNC shops use machines to complete their deburring and polishing processes, resulting in machined parts with rough edges and tiny, uncleaned holes. The CNC machines at Owens Industries are anything but “normal.” We know deburring is as important of a process as the machining itself. For the highest precision, attention to detail and accuracy must be applied from the start of a job to its completion.
Owens Industries has applied this attention to detail to every component machined in our Wisconsin facility. Our deburring department has 30 X Power Magnification Microscopes at every deburring station, backed by trained employees skilled in microdeburring.
View our Success Gallery to see our work!
Benefits of Deburring
Deburring, or the process of removing burrs or rough edges from the surface of a workpiece, offers several benefits.
- Improved fit and function: Burrs can cause issues with the fit and function of a workpiece, such as difficulty in assembling parts or interference with other components. Removing burrs ensures the workpiece fits and functions properly.
- Enhanced safety: Burrs can be sharp and potentially dangerous, especially on components that are handled frequently. Removing burrs helps to reduce the risk of injury and improve the overall safety of the workpiece.
- Increased efficiency and productivity: Burrs can cause delays in production and increase the time and effort required to assemble and use a workpiece. Removing burrs can help to streamline the manufacturing process and increase efficiency and productivity.
- Improved appearance: Burrs can negatively impact the appearance of a workpiece, making it look unfinished or unprofessional. Removing burrs helps to improve the overall appearance of the workpiece and enhance its visual appeal.
- Enhanced quality control: Removing burrs is an important step in the quality control process, as it helps to ensure the workpiece meets the required standards and specifications. This can help to reduce the risk of defects and improve customer satisfaction.
Types of Burrs
Several types of burrs can occur on the surface of a workpiece as a result of machining or other manufacturing processes.
- External burrs: Burrs that protrude from the surface of the workpiece and can be felt with the fingers. External burrs are typically the easiest to remove and are often removed using hand tools or automated deburring equipment.
- Internal burrs: Burrs that are located inside a hole or opening in the workpiece and are not visible from the outside. Internal burrs can be more difficult to remove and may require specialized deburring tools or techniques.
- Edge burrs: Burrs that occur on the edges of the workpiece and are often caused by cutting or grinding processes. Edge burrs can be difficult to remove and may require deburring tools with fine or flexible points to access the burr.
- Fillet burrs: Small, rounded burrs that occur at the corners or edges of the workpiece. Fillet burrs are often caused by the use of high-speed cutting tools and may be difficult to remove without damaging the surrounding material.
- Flank burrs: Burrs that occur on the flanks, or sides, of the workpiece. Flank burrs are typically caused by the use of high-speed cutting tools and can be difficult to remove without damaging the surrounding material.
Materials
Common Materials We Deburr
Owens Industries excels in deburring services with extensive experience in treating parts made from various materials. Our expertise covers a range of materials commonly used in manufacturing.
- Brass
- Copper
- Stainless Steel
- Tool Steel
- Alloy Steel
- Aluminum
- Hastelloy
- Inconel
- Invar
- Maraging Steel
- Titanium
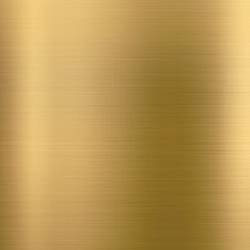
Brass
Brass is a metal known for its easy machinability and good electrical conductivity. It is ideal for applications requiring low friction, such as gears, locks, and musical instruments.
Brass | UNS Designation | DIN Designation | Alternative Designation |
---|---|---|---|
C36000 | UNS C36000 | CUZN39PB3 | CuZn39Pb3 |
C46400 | UNS C46400 | CuZn38Al | Naval Brass |
C93200 | UNS C93200 | Saems 660 | Bearing Bronze |
C48500 | UNS C48500 | CuZn39Sn1 | Leaded Muntz Metal |
C26000 | UNS C26000 | CUZN30 | Cartridge Brass |
C37700 | UNS C37700 | CUZN40PB2 | Forging Brass |
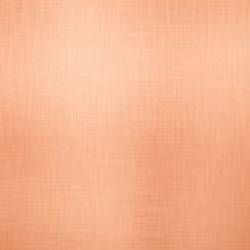
Copper
Copper is excellent at conducting heat and electricity, making it perfect for electrical uses like busbars and wire connectors. It is easily recognized by its shiny reddish-orange color and is also used in plumbing and roofing.
Copper | UNS Designation | DIN Designation | Alternative Designation |
---|---|---|---|
C11000 | UNS C11000 | Cu-ETP | Electrolytic Tough Pitch (ETP) Copper |
C10100 | UNS C10100 | OF-OK | Oxygen-Free Electronic (OFE) Copper |
C10200 | UNS C10200 | OF-Cu | Oxygen-Free (OF) Copper |
C28000 | UNS C28000 | CuZn40 | Muntz Metal |
C14500 | UNS C14500 | TeCu | Tellurium Copper |
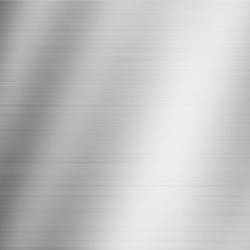
Stainless Steel
Stainless steel is known for its strength, heat, and corrosion resistance, along with its durability and attractive appearance. These qualities make it suitable for a wide range of uses, including kitchenware, medical instruments, and construction.
Stainless Steel | UNS Designation | DIN Designation | Alternative Designation |
---|---|---|---|
316L | UNS S31603 | X2CrNiMo17-12-2 | Stainless Steel 316L |
304 | UNS S30400 | X5CrNi18-10 | Stainless Steel 304 |
17-4 PH | UNS S17400 | X5CrNiCuNb16-4 | Stainless Steel 17-4 PH |
303 | UNS S30300 | X8CrNiS18-9 | Stainless Steel 303 |
420 | UNS S42000 | X20Cr13 | Stainless Steel 420 |
440C | UNS S44004 | X105CrMo17 | Stainless Steel 440C |
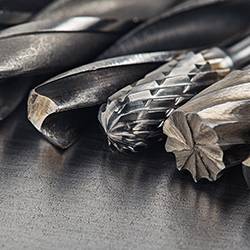
Tool Steel
Tool steels are hard, stiff, and resistant to abrasion, making them perfect for manufacturing industrial tools. Their robustness is essential for cutting, drilling, and molding applications in various industries.
Tool Steel | UNS Designation | DIN Designation | Alternative Designation |
---|---|---|---|
D2 | UNS T30402 | 1.2379 | X155CrVMo12-1 |
M2 | UNS T11302 | 1.3343 | HS6-5-2C |
A2 | UNS T30102 | 1.2363 | X100CrMoV5-1 |
S7 | UNS T41907 | 1.2355 | 50CrMoV13-15 |
O1 | UNS T31501 | 1.2510 | 100MnCrW4 |
H13 | UNS T20813 | 1.2344 | X40Cr |
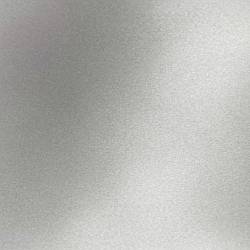
Alloy Steel
Alloy steels include additional elements beyond carbon, which improve their hardness, toughness, and resistance to fatigue and wear. These steels are widely used in construction, automotive, and machinery due to their enhanced properties.
Alloy Steel | UNS Designation | DIN Designation | ISO Designation |
---|---|---|---|
4140 | 1.7225 | 708M40 | 42CrMo4 |
4340 | 1.6565 | 817M40 | 40NiCrMo6 |
8620 | 1.6523 | 805M20 | 20NiCrMo2 |
52100 | 1.3505 | 100Cr6 | SUJ2 |
4142 | 1.7227 | 708M40T | 41CrMoS4 |
6150 | 1.8159 | 735A51 | 50CrV4 |
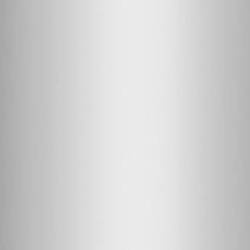
Aluminum
Aluminum alloys are lightweight and strong, with excellent thermal and electrical conductivity. They are also resistant to corrosion and can be anodized for added protection, making them ideal for aerospace and packaging industries.
Aluminum Alloy | UNS Designation | DIN Designation | ISO Designation |
---|---|---|---|
7075-T651 | 3.4365 | 76528 | AlZn5.5MgCu |
6082-T651 | 3.2315 | 64430 | AlSi1MgMn |
6060 | 3.3206 | EN AW-6060 | AlMgSi |
5052 | EN AW-5052 | 3.3523 | AlMg2,5 |
2017A | 3.1325 | 24530 | AlCu4MgSi |
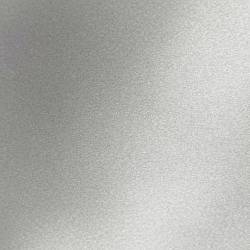
Hastelloy
Hastelloy is a group of nickel alloys known for their high resistance to corrosion, pitting, and stress-corrosion cracking. They are often used in harsh environments like chemical processing and aerospace, where durability is crucial.
Hastelloy | UNS Designation | DIN Designation | Alternative Designation |
---|---|---|---|
C276 | UNS N10276 | 2.4819 | NiMo16Cr15W |
C22 | UNS N06022 | 2.4602 | NiCr21Mo14W |
B-2 | UNS N10665 | 2.4617 | NiMo28 |
X | UNS N06002 | 2.4665 | NiCr22Fe18Mo |
C2000 | UNS N06200 | 2.4675 | NiCr23Mo16Cu |
G-30 | UNS N06030 | 2.4603 | NiCr29Mo9Fe |
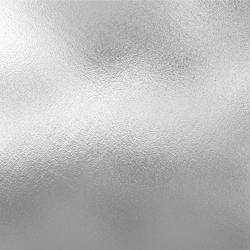
Inconel
Inconel is a strong, corrosion-resistant nickel alloy, ideal for challenging aerospace applications. It can withstand extreme temperatures and pressures, making it suitable for jet engines and gas turbines.
Inconel | UNS Designation | DIN Designation | Alternative Designation |
---|---|---|---|
718 | UNS N07718 | 2.4668 | NiCr19Fe19Nb5Mo3 |
625 | UNS N06625 | 2.4856 | NiCr22Mo9Nb |
600 | UNS N06600 | 2.4816 | NiCr15Fe |
X-750 | UNS N07750 | 2.4669 | NiCr15Fe7TiAl |
601 | UNS N06601 | 2.4851 | NiCr23Fe |
725 | UNS N07725 | 2.4668 | NiCr19Fe19Nb5Mo3 |
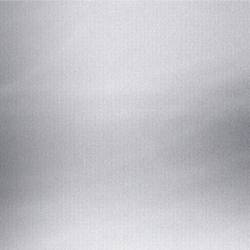
Invar
Invar is a nickel alloy with very low thermal expansion, making it highly stable and perfect for precision applications such as instrumentation and aerostructure molds. It is also used in scientific instruments where dimensional stability is critical.
Invar | UNS Designation | DIN Designation | Alternative Designation |
---|---|---|---|
36 | UNS K93600 | 1.3912 | FeNi36 |
42 | UNS K94200 | 1.3917 | FeNi42 |
48 | UNS K94800 | 1.3922 | FeNi48 |
32-5 | UNS K94610 | 1.3911 | FeNi32-5 |
42-6 | UNS K94620 | 1.3913 | FeNi42-6 |
46 | UNS K94630 | 1.3914 | FeNi46 |
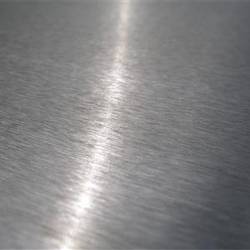
Maraging Steel
Maraging steels are ultra-high-strength steels that are easy to machine and weld without causing distortion. They gain their exceptional hardness and toughness from a special heat-treating process, making them suitable for aerospace and tooling applications.
Maraging Steel | UNS Designation | DIN Designation | Alternative Designation |
---|---|---|---|
200 | UNS K93120 | 1.6359 | 20Ni Maraging Steel C200 |
250 | UNS K92890 | 1.6358 | 18Ni Maraging Steel C250 |
300 | UNS K93120 | 1.6354 | 18Ni Maraging Steel C300 |
350 | UNS K93160 | 1.6356 | 18Ni Maraging Steel C350 |
400 | UNS K91460 | 1.6352 | Custom 465 Stainless |
500 | UNS K92810 | 1.6354 | Custom Age 625 Plus |
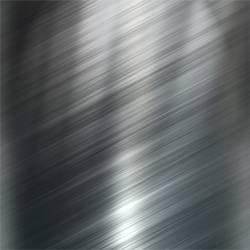
Titanium
Titanium is a lightweight metal with excellent strength, low thermal expansion, and high corrosion resistance. Its ability to be sterilized and its biocompatibility make it unique, especially in medical implants and aerospace components.
Titanium Grade | UNS Designation | DIN Designation | Alternative Designation |
---|---|---|---|
5 (Ti-6Al-4V) | UNS R56400 | 3.7165 | Ti-6Al-4V |
2 | UNS R50400 | 3.7035 | CP Titanium |
23 (Ti-6Al-4V ELI) | UNS R56401 | 3.7165 | Ti-6Al-4V ELI |
9 (Ti-3Al-2.5V) | UNS R56320 | 3.7195 | Ti-3Al-2.5V |
7 (Ti-0.2Pd) | UNS R52400 | 3.7235 | Ti-0.2Pd |
12 (Ti-0.3Mo-0.8Ni) | UNS R53400 | 3.7105 | Ti-0.3Mo-0.8Ni |
Industries
Industries Served by Owens Industries
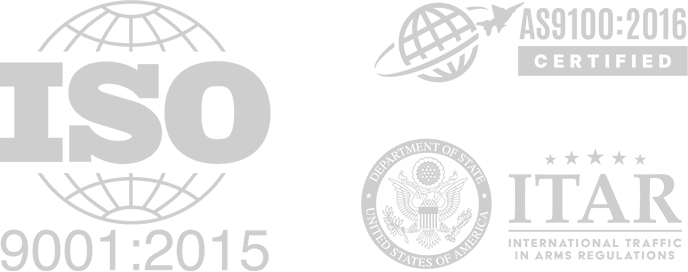

Deburring Services Across the United States
Choose Owens Industries for all your CNC machining needs. From discussing your design with our manufacturing engineers, through the 5-axis or EDM machining process, to by-hand deburring, Owens will be completely dedicated to providing services with the highest precision results.
Contact our Wisconsin Machine Shop to learn more about our available CNC machining capabilities and what sets Owens apart from our competitors.
FAQ
Deburring Frequently Asked
Questions
What is deburring metal?
Deburring metal involves removing the rough edges, called burrs, from a workpiece as a result of the CNC machining process. Deburring metal is essential to make certain parts function properly.
How do you deburr metal parts?
Deburring metal parts involves removing burrs with special deburring tools, either by hand or with automated deburring machines.
Why is deburring necessary?
Deburring is necessary to remove functionality problems on machined parts caused by the CNC machining process. Deburring metal also produces smooth parts without sharp edges for safer handling.
What is a deburr technician?
A deburring technician is a specially trained worker who carefully and precisely removes burrs from a machined metal product or part.
Is metal deburred by hand?
Many machine shops use grinders and other imprecise tools to deburr their parts. Owens has a precision deburring department that uses 30x microscopes to ensure all our parts are accurately deburred.