Case Study
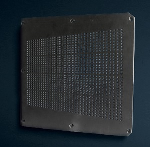
Wisconsin Machine Shop Achieves What Other Machine Shops Worldwide Could Not
Complex Optical Switch Machined with the Highest Precision and Accuracy
For $3 billion a large telecom company acquired a small company with 100 employees. This company had come up with a design for a purely optical switch. Imagine the prospects of this brand new technology – a switch with pure photon based switching would be phenomenally faster than the fiber optic silicon based switches.
The central (and critical) component of this purely optical switch was a collimator. The collimator required 1000 small holes - each hole angled differently than the proceeding one, each requiring a cylindrical and tapered inside diameter, and each hole had to focus on one focal point four feet away, with a positional accuracy of 2 microns each. The angular accuracy was about 20 arc seconds at four feet.
This company searched the world over for a CNC machine shop capable of producing such a complex component. They had prototypes made by companies in the USA, Germany, and Japan but none of these CNC shops could achieve the accuracy specified for the collimator. When Owens Industries approached this company with confidence that we could produce the component they needed, they were skeptical that a Wisconsin machine shop could achieve the precision they were searching the world over for. (They were in for a surprise.)
A Lifetime of Machining Experience = Solutions to Your Complex Component Problems
Lando, one of our key CNC machinists, played a lead role in determining the best course of action for machining the collimator. (Lando has been with Owens Industries for 35 years – hired as a teenager, this is the only job Lando has had in his lifetime. With his level of experience, he can practically bite into a metal and figure out the best way to machine it – we have more sophisticated methods of determining the machinability of complex alloys of course.)
Lando decided using our brand new 5 Axis machine would produce the results the collimator required. We separated the 5 Axis machining room from the rest of the shop and installed auxiliary HVAC systems to maintain the temperature of the room even more precisely. Then we installed external auxiliary chillers to further stabilize the coolant temperature.
Lando is nothing if not precise – he made sure the kinematics were exact, and insisted that the manufacturer re-calibrate the temperature compensation curves. After driving the machine tool supplier absolutely crazy, Lando achieved the perfect temperature compensation curves - doing a dry run on the machine over the weekend and splashing its work envelope with coolant to ensure everything would work properly during the real production of the collimators.
It was decided that the other machine shops used the common practice of drilling and reaming to produce the collimator. With further evaluation, Lando deduced the drill would walk at the exit point of the metal (the drill would deflect from the intended center-line of the bore, misplacing the hole). The solution was to drill a smaller hole first, then use a bore to straighten the “micron drift” of the drill, then use a tapered reamer to finish the hole.
Ultra Precise Machining Results Making Extremely Happy Clients
We admit that we do not have the capability to measure the tolerances specified for this collimator, but neither did the customer. The only way they could measure the accuracy was to actually assemble and test the collimator with photons. We are happy to report, 99% of our collimators passed the test! And we have had a happy customer ever since.
Contact our 5 Axis machinists to learn more about this case or to discuss your parts needs.
Get high-quality manufactured CNC components made with the best materials from Owens Industries.